Reliability Improvement
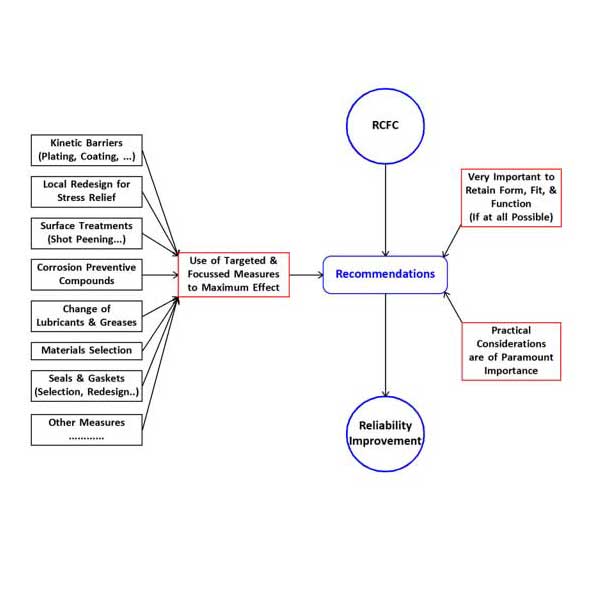
Illustration 1: Our preferred flow for developing reliability improvement recommendations. Click to enlarge.
DTB’s client wanted the capability to predict the degradation of a variety of items in shelf-storage configurations. The client also needed to predict life improvement/degradation with alterations in packaging configurations.
Our solution was to develop a conceptual framework to include the aging of the packaging and contents, as well as the interaction effects between the packaging and contents. We also designed and performed aging protocols, including a comprehensive data analysis, to develop a capability to predict degradation kinetics by coupling Arrhenius and empirical components.
Accelerated Aging Testing Services
DTB uses a highly structured failure analysis-based approach for reliability improvements. Typically, the approach results in the development of a detailed root cause failure cascade (RCFC), which becomes the basis for developing reliability improvement recommendations.
When developing root cause failure cascade (RCFC) recommendations, we make certain that the failure is not shifted to another component or location, which can degrade reliability due to an added element of uncertainty. We also ensure that the recommendations are thoroughly practical – otherwise, they may never get implemented. Ideally, the form, fit, and function should remain unaltered, which may not be as restrictive as it may first appear, since failures can be eliminated through the targeted and judicious use of measures, such as materials selection; kinetic barriers, including coating/plating treatments; surface treatments, such as shot peening; redesign or better selection of seals and gaskets; elimination of stress raisers; and revised maintenance practices, including the use of corrosion preventive compounds.
Developing Reliability Improvement Recommendations
Many times, there is a need for proving the effectiveness of reliability improvement recommendations prior to field implementation. This is significant because of two stringent requirements: (1) the testing must be conducted in a manner that replicates, with high fidelity, the service environment; and (2) the testing must utilize protocols that accelerate the process while maintaining test validity.
In general, when developing the test protocol(s), it is important to involve the failure analysis team because they are very conversant with weak links in the system, including their response to stresses, the physical characteristics of various nominal failure modes, and the methods and techniques to be utilized for tracking system failure(s). It is also important to test the original and enhanced assemblies side-by-side so that reliability improvements can be quantified and the effect(s) of any test anomalies can be eliminated without ambiguity.
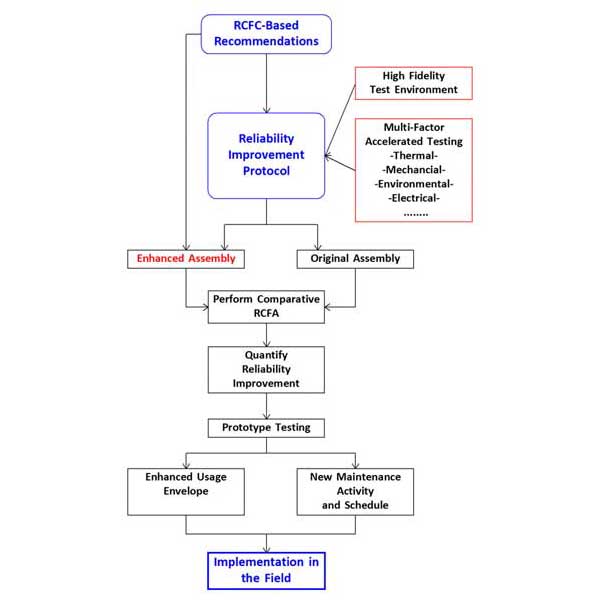