Maintenance Planning & Reliability Overview
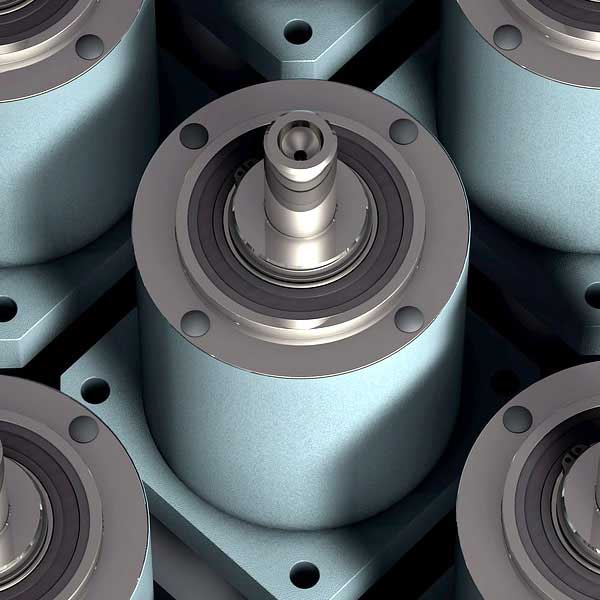
Maintenance planning uses analytical methodologies to determine when an item will need to be replaced, repaired, or discarded based on cost considerations and operational readiness requirements. Major platforms include complex systems that contain assemblies, sub-assemblies, and components, which are organized into several levels of possible repair decisions.
Dayton T. Brown Inc.’s systems perform analyses to determine optimal repair and maintenance criteria – aiming to minimize overall system life cycle costs. We report the results of the analyses according to commercial best practices, as defined by SAE (TA-STD-0017) and military logistics standards (MIL-STD-1388-2B and/or GEIA-STD-0007).
Logistics personnel examine all of the required elements from specific selection sets to ensure that the maintenance planning is documented correctly.
Maintenance Planning & Reliability Services
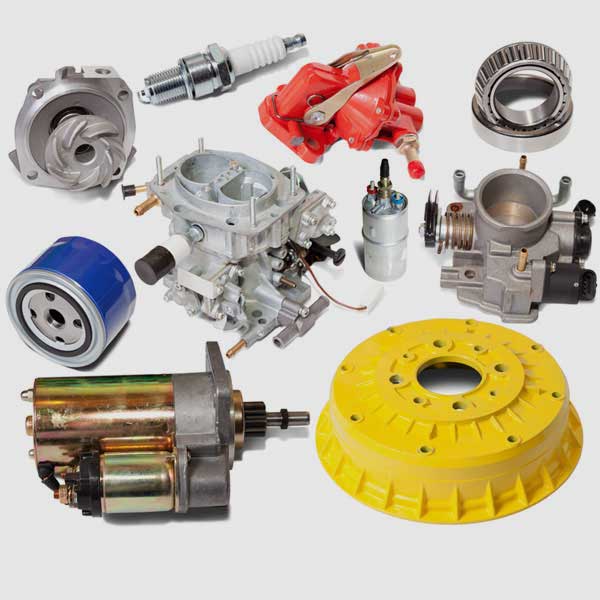
Reliability Engineering
Reliability is defined as the probability of failure, the frequency of failures, or, in terms of availability, a probability derived from reliability and maintainability. Reliability engineering is an engineering discipline that studies, evaluates, and assesses the life cycle support of a system or component to perform under stated conditions for a specified period of time. Maintenance and maintainability are an integral component of this type of engineering.
Reliability engineering for complex systems requires a different, more elaborate systems approach than for non-complex systems. Reliability analysis has important ties that correspond with:
- Functional analysis
- Storage
- Specification requirements
- Spare parts
- Information delivery
- Operations research
- Manufacture / Quality
- Human factors
- Maintenance
- Technical documentation
- Transport
- Work skills training
Effective reliability engineering requires experience, broad engineering skills, and knowledge of many different fields of engineering. Reliability plays a key role in the cost-effectiveness of systems, with reliability engineering focusing on the costs of failure that may be caused by system downtime, spares, repair equipment, personnel, and warranty claims.
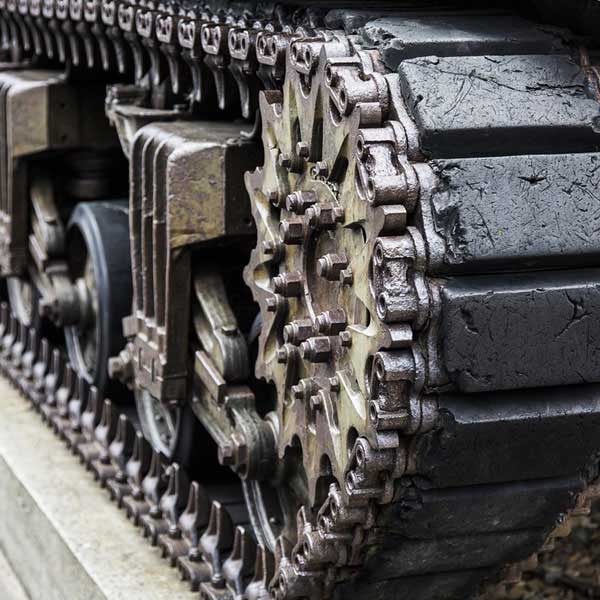
Level of Repair Analysis (LORA)
The reason to perform LORA is to establish the most cost-effective repair level or discard alternative in order to perform maintenance actions. Maintenance planning relies on LORA as a function of the acquisition process. LORA is used by the Department of Defense (DoD) as an analytical methodology in order to determine when an item will need to be replaced, repaired, or discarded based on cost considerations and operational readiness requirements.
LORA optimizes the support system in terms of Life Cycle Costs (LCCs), readiness objectives, design for discard, maintenance task distribution, support equipment and Automatic Test Equipment (ATE), and manpower and personnel requirements.
Complex engineering systems contain thousands of assemblies, sub-assemblies, and components, each organized into several levels of indenture with a number of possible repair decisions. LORA seeks to determine an optimal provision of repair and maintenance facilities in order to minimize overall system LCCs.
It is important to review all of the details in order to provide clients with actionable information. DTB addresses this aspect so that you can focus on the other areas of your business.
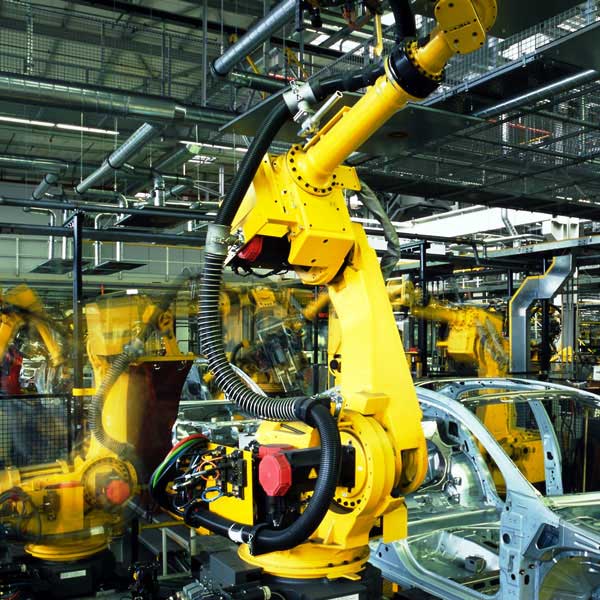
Benefits of Maintenance Planning
Our clients benefit from Maintenance Planning as it provides important analysis for decision-making over the life of a program, as well as reduces total Life Cycle Costs (LCCs). Some of the other benefits of Maintenance Planning include:
- Defining the actions and support necessary to ensure that the system attains the specified system readiness objectives with minimum LCCs
- Setting up the specific criteria for repair, including Built-In Test Equipment (BITE), testability, reliability and maintainability, support equipment and Automatic Test Equipment (ATE), and manpower and personnel requirements
- Stating the specific maintenance tasks to be performed on the system
- Defining the actions and support required for fielding and marketing the system
- Addressing any warranty considerations